
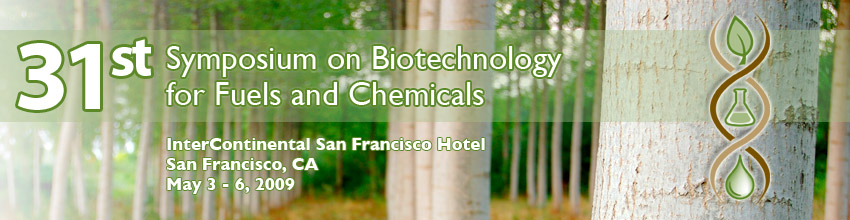
Sunday, May 3, 2009
3-92
Improved One-Step Steam Pretreatment of Softwood with Time-dependent Temperature Profile for Bioethanol Production
Sanam Monavari, Mats Galbe, and Guido Zacchi. Chemical Engineering, Lund University, P.O.Box 124, SE- 22100, Lund, Sweden
At a time when natural petroleum resources are almost on the verge of depletion and concern about climate change is increasing, the potential of lignocellulosics for production of bioethanol is well recognized. Ethanol can be produced from biomass through enzymatic hydrolysis and fermentation. However, pretreatment of naturally resistant cellulosic material is necessary to achieve a high ethanol yield. Pretreatment, as a crucial step for enzymatic digestibility of biomass, is among the most expensive process steps.
To date, two-step, dilute-acid pretreatment of softwood (using SO2), with separation and washing of the material between steps, has shown to result in the highest sugar and ethanol yields. In the first step, hemicellulose is hydrolyzed at milder conditions. The breakdown of the recalcitrant structure of cellulose is the aim of the more severe second acid-hydrolysis step. However, in an industrial process, filtration and washing of material between steps are difficult, as they should be performed at high pressure to avoid heat losses. Washing also leads to dilution of sugars. Furthermore, two-step dilute-acid pretreatment with separation and washing is energy demanding and requires higher capital costs.
In the current study, a new pretreatment reactor, with a novel time-dependent temperature profile, combining the two-step process into a one-step pretreatment, is being investigated. The aim is to improve sugar and ethanol yields through enhancing the digestibility of the cellulose chain, lowering the dilution of sugars, and minimizing sugar degradation products. Accordingly, the efficiency of different pretreatment experiments is assessed by running fermentability tests (SSF) on the pretreated slurry.
To date, two-step, dilute-acid pretreatment of softwood (using SO2), with separation and washing of the material between steps, has shown to result in the highest sugar and ethanol yields. In the first step, hemicellulose is hydrolyzed at milder conditions. The breakdown of the recalcitrant structure of cellulose is the aim of the more severe second acid-hydrolysis step. However, in an industrial process, filtration and washing of material between steps are difficult, as they should be performed at high pressure to avoid heat losses. Washing also leads to dilution of sugars. Furthermore, two-step dilute-acid pretreatment with separation and washing is energy demanding and requires higher capital costs.
In the current study, a new pretreatment reactor, with a novel time-dependent temperature profile, combining the two-step process into a one-step pretreatment, is being investigated. The aim is to improve sugar and ethanol yields through enhancing the digestibility of the cellulose chain, lowering the dilution of sugars, and minimizing sugar degradation products. Accordingly, the efficiency of different pretreatment experiments is assessed by running fermentability tests (SSF) on the pretreated slurry.