
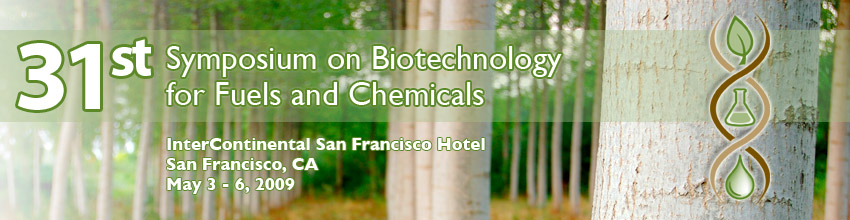
Tuesday, May 5, 2009 - 9:00 AM
7-03
Development and Deployment of Consolidated Bioprocessing for Production of Ethanol
Michael Ladisch1, Jim Flatt1, Alan Belcher1, Justin van Rooyen1, M.S. Sivasubramanian1, Don Dimasi1, Lee R. Lynd2, Charles Wyman3, David A. Hogsett1, Jerry Draeger4, Youngmi Kim5, Eduardo A. Ximenes6, and Nathan Mosier5. (1) Chief Technology Officer, Mascoma Corporation, 1380 Soldiers Field Road, Second Floor, Boston, MA 02135, (2) Thayer School of Engineering, Dartmouth College, 8000 Cummings Hall, Hanover, NH 03755, (3) University of California, Center for Environmental Research and Technology, 1084 Columbia Avenue, Riverside, CA 92507, (4) Frontier Renewable Resources, LLC, (5) LORRE/Ag. and Bio. Engineering, Purdue University, 500 Central Dr., West Lafayette, IN 47907, (6) Agricultural Engineering, Purdue University, Potter Engineering Center, 500 Central Drive, West Lafayette, IN 47907-2022
Consolidated Bioprocessing (“CBP”) employs single microorganism that simultaneously generates sugars and produces ethanol from wood and other forms of pretreated lignocellulosic biomass. Pretreatment opens up the structure of wood by disrupting the lignin seal and exposing cellulosic plant cell wall components. This enables CBP microorganisms to access the cellulosic constituents, hydrolyze them, and produce ethanol. The microorganisms not only ferment sugars to ethanol, but also generate the biocatalysts – enzymes – that are needed to break down cellulose into fermentable sugars. Mascoma’s research is combining naturally occurring metabolic activities into a single microorganism by modifying the fermentative pathways of nature’s most efficient processors of cellulose, including the thermophilic anaerobic bacterium, Cl. thermocellum, to produce high yields of ethanol from hardwoods and biomass feedstocks. In addition, the ability to modify the fermentative pathways of a thermophilic anaerobe to achieve high ethanol yield from sugars was previously demonstrated through metabolic engineering of T. saccharolyticum. The practical application of Consolidated Bioprocessing is based on combining new biotechnology and unique but established process engineering. We discuss the four basic steps convert wood to ethanol; (1) feedstock preparation (chipping); (2) simple pretreatment of wood to make it accessible to microbial action; (3) fermentation to ethanol; and (4) product separations for recovery of fuel-grade ethanol and lignin. The design of a commercial facility is being informed by pilot and demonstration scale validation of fermentation parameters and designs that have evolved from work of NREL, DOE and USDA sponsored programs in both the public and private sectors.
See more of Biorefinery Deployment
See more of The 31st Symposium on Biotechnology for Fuels and Chemicals (May 3-6, 2009)
See more of The 31st Symposium on Biotechnology for Fuels and Chemicals (May 3-6, 2009)