
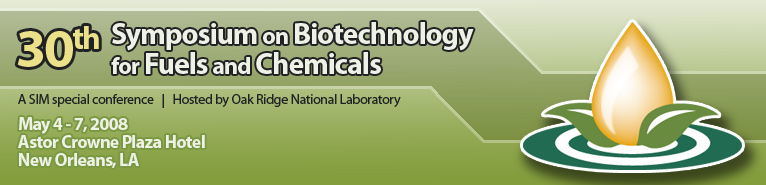
Monday, May 5, 2008
8-07
A Novel Pretreatment Process for Robust Bioconversion of Lignocellulose
J. Y. Zhu1, Gaosheng Wang2, Xuejun Pan3, Roland Glesiner1, and Donald L. Rockwood4. (1) USDA Forest Service, Forest Products Laboratory, One Gifford Pinchot Dr, Madison, WI 53726, (2) College of Chemcial Engineering and Material Sciences, Tianjin University of Science and Technology, TianJian, China, (3) Biological Systems Engineering, University of Wisconsin, 460 Henry Mall, Madison, WI 53706, (4) College of Agriculture and Life Science, Univeristy of Florida, Gainsville, FL
Pretreatment of feedstock is critical to achieve satisfactory conversion of lignocellulose. Several pretreatment processes have been developed and achieved some level of success. However, most existing pretreatment processes have two major pitfalls. First, the pretreatments are effective only on size reduced biomass feedstocks. As a result, these processes are unable to take the advantage of the softening effect of pretreatment on wood structure to reduce energy consumption for size reduction. The second, the existing processes produced low enzymatic hydrolysis (cellulose-to-glucose conversion) efficiency (<75%) when they are applied to softwood. Unfortunately, forestry is a significant source of biomass feedstock for biorefining, and softwood is the major species in several parts of the US, Canada and Scandinavia. This study demonstrated a novel pretreatment process (Patent application pending) for robust bioconversion of lignocellulose including softwood. Enzymatic cellulose hydrolysis of 90% was achieved within 24 hours with commercial enzymes for spruce (softwood) and short rotation eucalyptus (hardwood) after the pretreatment under mild conditions of chemical dosage, reaction time, and temperature. No significant delignification is required. Furthermore, the pretreatment provided near complete separation of hemicellulose form cellulose, which promised separate utilization of hemicellulose sugars. In addition, the pretreatment reduced the overall energy consumption for size reduction by 70%, to only about 150 Wh/kg for softwood.
See more of Poster Session Two
See more of General Submissions
See more of The 30th Symposium on Biotechnology for Fuels and Chemicals (May 4 -- 7, 2008)
See more of General Submissions
See more of The 30th Symposium on Biotechnology for Fuels and Chemicals (May 4 -- 7, 2008)