
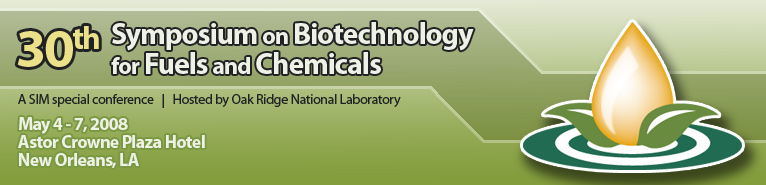
Wednesday, May 7, 2008 - 1:30 PM
11-01
MixAlco process: fuels and chemicals from biomass
Via “acid springing,” carboxylate salts are converted to carboxylic acids, which may be hydrogenated to primary alcohols (e.g., ethanol). Alternatively, thermal conversion produces ketones, which may be hydrogenated to secondary alcohols (e.g., isopropanol). If desired, the alcohols can be catalytically dehydrated to hydrocarbons, such as gasoline, diesel, or jet fuel.
The advantages of the MixAlco process follow:
· No sterility required in the fermentation
· No genetically modified organisms
· No enzyme costs
· Wide variety of feedstocks can be employed
· Wide variety of fuel and chemical products
· High energy density in fuels (secondary alcohols and hydrocarbons)
· Low capital cost
· Low product cost
Recent economic evaluations indicate that primary alcohols can be sold for about $1.13/gal (15% ROI, 10-yr depreciation, 15% working capital, $53/ton biomass cost). The capital cost is estimated to be about $0.82/annual gallon. A demonstration plant is under construction.
Web Page: www.terrabon.com/
See more of General Submissions
See more of The 30th Symposium on Biotechnology for Fuels and Chemicals (May 4 -- 7, 2008)