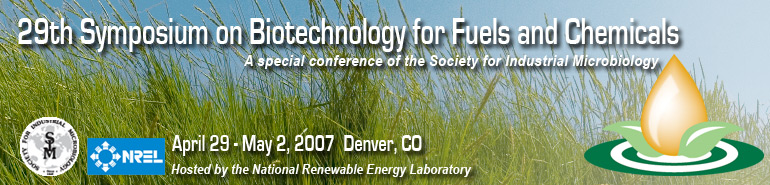
Monday, April 30, 2007 - 2:30 PM
3-04
Result and experience in the research plant of production of ethanol from lignocellulose
Marlene Mörtsell Sr., Torbjörn van der Meulen, Stefan Rännar, Anders Wingren, Tomas Brandberg, and Maria Edlund. SEKAB E-Technology, Box 286, SE-891 26 Örnsköldsvik, Sweden
The Ethanol Research and Development Plant is housed in SEKAB’s premises in Örnsköldsvik, Sweden , is built in cooperation between SEKAB and regional universities. The plant serves as a basis for development of production of ethanol from lignocellulose and has a capacity of 300-400 litres ethanol per 24 hours period. In order to manufacture this quantity, approximately 2 tonnes (dry weight) of woodchips or other raw material that contains lignocellulose is used.
The technology is based on hydrolysis of cellulose and hemicellulose, whereupon the sugar is released and fermented to ethanol, which is then distilled. In the plant it is possible to apply either diluted acid hydrolysis or enzymatic hydrolysis. Diluted acid hydrolysis is applied, sulphuric acid or sulphur dioxide, in a two stage process at temperatures around 170 - 210ºC. When enzymatic hydrolysis is applied, the material is first exposed to a mild diluted acid hydrolysis treatment after which enzymes hydrolyse the remaining cellulose. Both the dilute acid and enzymatic processes are currently being evaluated at the plant. The plant is flexible and there are significant feedback possibilities in the process flow. In the four fermenters, it is possible to apply either fed-batch or continuous technology. Initially, spruce wood chips are used, but other raw materials will also be studied.
The technology is based on hydrolysis of cellulose and hemicellulose, whereupon the sugar is released and fermented to ethanol, which is then distilled. In the plant it is possible to apply either diluted acid hydrolysis or enzymatic hydrolysis. Diluted acid hydrolysis is applied, sulphuric acid or sulphur dioxide, in a two stage process at temperatures around 170 - 210ºC. When enzymatic hydrolysis is applied, the material is first exposed to a mild diluted acid hydrolysis treatment after which enzymes hydrolyse the remaining cellulose. Both the dilute acid and enzymatic processes are currently being evaluated at the plant. The plant is flexible and there are significant feedback possibilities in the process flow. In the four fermenters, it is possible to apply either fed-batch or continuous technology. Initially, spruce wood chips are used, but other raw materials will also be studied.
Result and experiences with focus on the hydrolysis, both dilute acid and enzymatic, will be discussed.