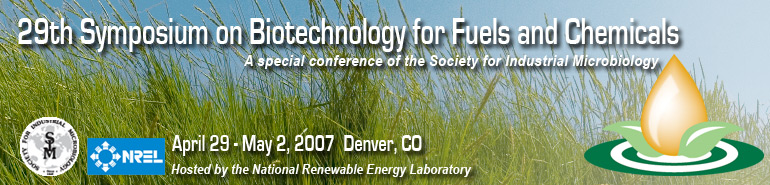
Wednesday, May 2, 2007 - 10:20 AM
5B-07
Pretreatment of ligno-cellulose with biological acid recycling (the Biosulfurol process)
Johan W. Van Groenestijn, TNO, P.O. Box 360, Zeist, 3700 AJ, Netherlands, Obbo Hazewinkel, Techno Invent, and Robert R. Bakker, Wageningen University and Research Centre.
A biomass pretreatment process is being developed based on contacting ligno-cellulosic biomass with 70% sulphuric acid at moderate temperatures and subsequent hydrolysis by adding water. In this process, the hydrolysate can be fermented yielding ethanol, while the sulphuric acid is partly recovered by anion-selective membranes before the fermentation process, and partly via biological sulphate reduction in the anaerobic wastewater treatment plant. The produced sulphide is recovered as H2S gas and chemically converted (burned) into SO2 and SO3 (by which heat is recovered as well) and subsequently into sulphuric acid. In this unique approach, the sulphuric acid is recycled to a large extent. In the project switchgrass and willow wood are tested as model substrates. The advantages of the process compared with other processes that convert lignocellulosic biomass into ethanol are:
· No enzymes are required. Pretreatment/hydrolysis processes that require enzymes anticipate a decrease of the enzyme prices, but with uncertain technical and economic feasibility.
· Broad range of biomass types can be used (e.g. wood, straw and grass).
· Relatively large and hard pieces of wood can be used.
· Pretreatment at room temperature allows the use of plastic construction materials.
· The low temperature used limits the production of inhibitory compounds such as furfural.
· The difference with other concentrated sulphuric acid pre-treatment processes is the application of novel sulphate recovery processes, made available through developments in other technology areas.
· Lower overall costs. Production costs ethanol from switchgrass will be between € 0.20 and € 0.30/l.
· No enzymes are required. Pretreatment/hydrolysis processes that require enzymes anticipate a decrease of the enzyme prices, but with uncertain technical and economic feasibility.
· Broad range of biomass types can be used (e.g. wood, straw and grass).
· Relatively large and hard pieces of wood can be used.
· Pretreatment at room temperature allows the use of plastic construction materials.
· The low temperature used limits the production of inhibitory compounds such as furfural.
· The difference with other concentrated sulphuric acid pre-treatment processes is the application of novel sulphate recovery processes, made available through developments in other technology areas.
· Lower overall costs. Production costs ethanol from switchgrass will be between € 0.20 and € 0.30/l.