
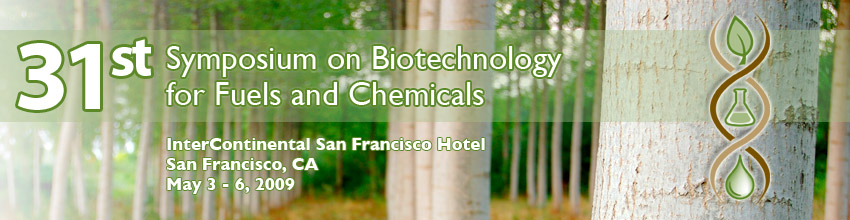
Monday, May 4, 2009 - 8:00 AM
3-01
On Size Reduction for Woody Biomass Conversion
In this study, we used various fiber fractionations, different chemical pretreatments, and mechanical milling (size reduction) processes to produce wood substrates with varied physical sizes, chemical structures and physical properties. We demonstrated a wet imaging technique to determine two dimensions of these woody fibrous substrates. The measured two dimensions were used to estimate the substrate specific surface by using a cylinder model for individual fibers. The determined substrate specific surface was related to the enzymatic hydrolysis cellulose conversion of the substrate. We also compared the effectiveness of different chemical pretreatments applied directly to wood chips (~2x3x0.5 cm) on reducing size-reduction energy consumption and enhancing enzymatic saccharification, so that the efficiencies of different chemical pretreatments and size-reduction processes can be compared objectively. It was found that Chemical pretreatment affects not only cellulose conversion efficiency, but also post-pretreatment size-reduction energy consumption and liquefaction of substrates during high solids enzymatic hydrolysis. The SPORL pretreatment process that we developed is the most efficient with cellulose conversion of over 90% and post-pretreatment wood chip size-reduction energy consumption of about 30 Wh/kg.