
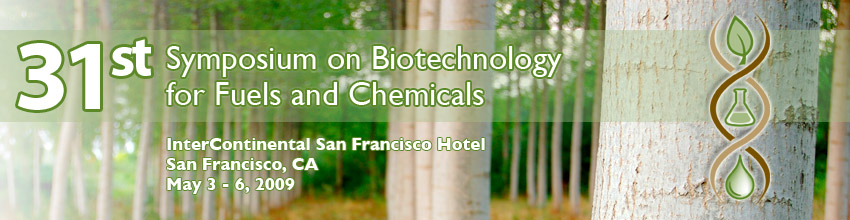
Sunday, May 3, 2009
3-94
Integrated High Throughput Pretreatment and Enzymatic Hydrolysis in 96 Well Plates
Michael Studer1, Jaclyn D. DeMartini1, Heather L. McKenzie2, and Charles E. Wyman3. (1) Chemical & Environmental Engineering, Center for Environmental Research and Technology, University of California, Riverside, 1084 Columbia Avenue, Riverside, CA 92507, (2) Department of Chemical & Environmental Engineering, Center for Environmental Research and Technology, University of California, Riverside, 1084 Columbia Ave, Riverside, CA 92507, (3) Center for Environmental Research and Technology, Bourns College of Engineering, University of California, Riverside, 1084 Columbia Avenue, Riverside, CA 92521
One of the aims of the BioEnergy Science Center is the engineering of advanced plants with reduced recalcitrance for sugar release. As this requires screening many different natural and genetically modified biomass types to identify those with lower recalcitrance for sugar release, a new high throughput (HTP) tool integrating pretreatment and enzymatic hydrolysis in the same multi-well configuration was developed. Water only or dilute acid pretreatment of 1% biomass slurries is performed in a custom-made 300μL 96 well plate made of metal to withstand heating to temperatures up to 180oC in a steam chamber, as well as to prevent corrosion. Furthermore, our so-called co-hydrolysis approach adds citric acid buffer, sodium azide, and enzyme directly to each well without separating the solid and liquid after pretreatment, with enzyme loadings based on original glucan and xylan content of the raw biomass. Next, the plate is incubated at 50oC for 72 hours, and the release of sugars is quantified by HPLC. To prove the feasibility of this concept, performance of co-hydrolysis was compared to that of conventional washed solids hydrolysis. The standard deviation in total sugar yields was only 4.1% across the 96 wells for combined pretreatment and co-hydrolysis, and yields for co-hydrolysis with the multi-well system were virtually identical to those with standard tube reactors as well as washed solids hydrolysis using standard vessels. Operational testing demonstrated that the custom-made well plates did not leak during pretreatment, and heat-up and cool-down required less than 45 seconds at an operating temperature of 180oC.